November 14, 2022
Prototype Volvo hydrogen fuel cell electric truck. volvo trucks
With the threats of climate change becoming a stark reality —including 6,000 temperature records set around the U.S. in July 2022—the efforts to build a clean energy economy must look to any and all options for replacing fossil fuels. Wind and solar are increasingly competitive. They join the long-standing alternative energy sources of nuclear and hydropower (and to a lesser extent geothermal).
But there remains the tantalizing prospect of widespread use of hydrogen—nature’s most abundant element, found everywhere around us, including paired two-atoms-to-one with oxygen in water. The problem is, substantial energy is required to create free hydrogen, including using electricity to crack the chemical bonds in water through electrolysis.
That energy penalty places great limits on hydrogen’s usefulness. Toyota, Hyundai and a few other manufacturers have built hydrogen-powered vehicles, employing fuel cells that strip electrons from hydrogen as it combines with oxygen.
But hydrogen vehicles—known as fuel cell electric vehicles (FCEV)—just can’t compete in terms of overall efficiency with battery electric vehicles for passenger cars. Battery electric systems have all but won out in the consumer vehicle market, led by Tesla.
But other factors come into play that favor hydrogen to cleanly power the largest vehicles such as long-haul trucks. As a result, long-haul trucking remains a potential leading-edge application for hydrogen, one that could lay the ground for wider applications of hydrogen throughout a clean energy economy. The trucks would reduce a large share of greenhouse gases generated by the transportation sector—one-third of the total—along with other harmful air pollutants that beset populations in heavily-travelled truck corridors.
Heavy Loads
Fuel cells offer the prospect of vehicles that generate their own electricity without long periods of charging and emit only water from their tailpipes. The devices have a storied history including use in generating power for the 1969 Apollo moon landing mission while providing drinking water for the crew.
The problem is that 70 percent of the potential energy of free hydrogen is lost before it ever makes it to vehicle wheels—mainly due to the energy needed for electrolysis, compression of the gas for storage and transport and fuel cell processing. In contrast, relatively little energy—about 30 percent—is lost in transporting wind or solar energy over the power grid to charge batteries and discharging the batteries to power electric motors.
Tesla founder Elon Musk expresses open contempt for all things hydrogen, calling fuels cells “a load of rubbish” and “fool sells.” Volkswagen has rejected further hydrogen development for its cars. Its company statement quotes scientist Dietmar Voggenreite: “No sustainable economy can afford to use twice as much renewable energy to drive fuel cell cars instead of battery-powered vehicles.”
Even so, powering big rigs with batteries is problematic. Batteries are heavy. According to CNET, a long-range Tesla Model S sedan weighs 4,560 pounds—510 pounds more than a comparable gas-driven BMW. Some electric cars need special rear tires to accommodate the extra weight. This weight penalty is not a big deal when shuttling kids around town or hauling small packages in a delivery van. But it is a very big deal when powering big rigs that can carry payloads of 16 to 20 tons, operating for long periods, often over challenging terrain and through variable weather conditions. Those trucks typically travel 75,000 miles per year or about 300 to 600 miles per day.
A Carnegie Mellon study found a 600-mile capable battery pack would weigh more than 18 tons, significantly more than the cargo that many trucks carry. When the batteries discharge, the trucks would end up hauling around heavy useless weight. In contrast, studies have found that hydrogen fuel cells have an energy-to-weight ratio 10 times greater than lithium-ion batteries.
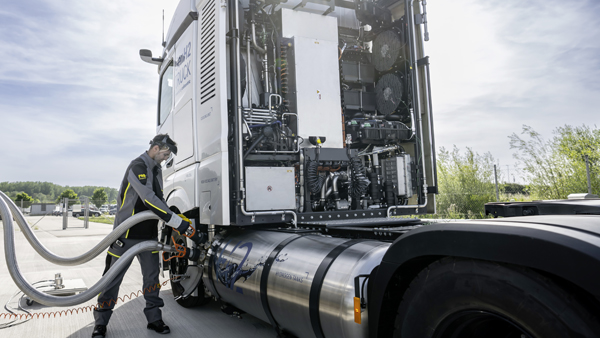
Daimler's prototype fuel cell truck uses super-cooled hydrogen. daimler truck
Power Demand
Another significant factor for battery-powered trucks is charging time. A Tesla or other battery electric passenger car is most cost-effectively charged overnight. A level-4 fast charger can get some electric vehicles to an 80 percent charge in around 30 minutes. That’s for a battery of 40 to 120 kilowatt hours (kwh) (a measure of battery capacity). A large truck battery would need four times that—400 to 750 kwh—requiring hours on a fast charger.
That adds up to a real time penalty for electric trucks. Many drivers are on the clock and can’t afford long stretches of downtime. Refueling with hydrogen would take about 15 minutes, about the same for diesel trucks.
The need for long charging could also cause big problems for the electricity grid. Lars Stenqvist, Executive Vice President of Volvo Group Trucks Technology, speaking on Robert Llewellyn’s Fully Charged YouTube channel, pointed out that accommodating 50 or more trucks charging simultaneously for hours or overnight at a truck stop could draw huge amounts of power and require extensive new infrastructure and grid upgrades. Multiplied by hundreds of truck stops across Europe, the nightly demand he said could approach a gigawatt—“the size of a nuclear plant.”
While hydrogen distribution systems for trucks are mostly still at the testing stage, fueling facilities at truck stops could be supplied with hydrogen by tanker truck as diesel is now.
Battery Research
Despite the challenges they face, battery electric systems are still very much in the running for powering the future long-haul truck market. Tesla and Volkswagen’s Scania division are betting on battery advances to make fully electric trucks competitive, drawing on intensive research underway in their own facilities, in start-up companies and academic labs. These efforts seek to create smaller, more energy-dense batteries. Much research in recent years has been focused on the holy grail of “solid state” batteries. The latest advances seek to use sulfur to achieve three times the energy density of current batteries, with more readily available materials.
The advances might remove much of the energy and weight penalties of batteries for heavy duty vehicles. Musk, with typical bombast, is promising Tesla’s first electric big rig deliveries in the next couple years—though the goal post keeps moving—produced with the company’s own battery factories and drawing on its record of delivering increased energy density in batteries used in its sedans.
Meanwhile a growing number of freight operators—including giants like PepsiCo and Amazon—are purchasing electric battery-powered light and medium duty trucks for local delivery, mostly charging them overnight at depots. As the base of the smaller electric trucks grows, many companies may be inclined to make the shift to larger electric vehicles for other needs, even if they have operational disadvantages in the short term—especially if fast-moving technology delivers cost advantages.

Daimler's truck fuel cell stack—about the size of a diesal engine. daimler truck
Hydrogen Research
But hydrogen systems are very much in the technology race, with similarly intensive research, much of it backed by the federal government with public sector involvement. A caveat for all these efforts is that the systems depend on the eventual availability of reasonably priced green hydrogen—that is, hydrogen extracted from water using energy from wind, solar or other sustainable sources, rather than from natural gas, which is the source for nearly all hydrogen(called grey hydrogen) currently in use. Incentive programs in the federal Inflation Reduction Act, by some accounts, will be a game changer for boosting green hydrogen production (see sidebar).
In the transportation sector, the U.S. Department of Energy is supporting basic research and engineering through a Million Mile Fuel Cell Truck initiative, a consortium of five national labs along with 20 or more academic and industry partners.
Why “Million Mile?” According to Rod Borup, staff scientist at Los Alamos National Laboratory and co-director of the program the life of a truck can stretch a million miles or more, compared to perhaps 200,000 miles for passenger cars. Achieving that level of durability in fuel cells and on-board systems—including under often extreme temperatures and heavy power demands—is a key objective of the project.
The program is also looking for the most efficient yield of energy from a variety of materials and catalysts in fuel cells—at the heart of which is the membrane electrode assembly which chemically separates protons and electrons in hydrogen to generate electricity. “There is a lot more that can be done to optimize fuel cells,” said Borup.
Another Department of Energy-supported consortium, the Electrocatalysis (ElectoCat) Consortium, is focusing on reducing reliance on expensive platinum in fuel cell catalysts—with a goal to reduce it to the level used in automobile catalytic converters.
Testing
Drawing on the wide-ranging research underway, manufacturers are designing, building and testing prototype vehicles. They seek to position themselves to capture a share of the potentially transformed heavy duty truck market later in the decade. Furthest along are companies in China, Japan and Europe—reflecting the level of government commitments there to cleaning up the trucking sector.
In Europe, truck makers Volvo and Daimler have joined forces in a venture called Cellcentric to develop an efficient fuel cell system and are backing the organization H2Accelerate, which is promoting a plan for truck deployment continent-wide. It begins in a “learning” phase involving several hundred vehicles on the road through 2025, leading to “full industrialization” by 2030 with tens of thousands of hydrogen trucks competitive with diesel vehicles.
The Daimler prototype relies on super-cooled liquid hydrogen which is more energy-dense and requires smaller fuel tanks than compressed hydrogen gas (though the cooling requires more up-front energy). Like other prototypes, the truck has a high voltage battery to regulate electricity from the fuel cells to the motors and capture braking energy. Both Daimler and Volvo are touting a 1,000-km (621-mile) range for their vehicles which makes possible refueling at widely dispersed hydrogen-supplied truck stops along highways.
American companies are not sitting on the sideline. Rochester, New York-based Hydron has provided its vehicles—built on retrofitted standard semi-truck chassis—to Europe, China and Australia and has made agreements to deploy up to 1,000 vehicles to service ports in the Netherlands. Seattle-based Kenworth has joined with Toyota in testing prototypes at the Port of Los Angeles (see sidebar).
Nikola Motors of Phoenix is rebounding under new management after crippling legal and U.S. Securities and Exchange Commission challenges over stock manipulation by its founder. Its long-haul trucks are slated for full production in 2024.
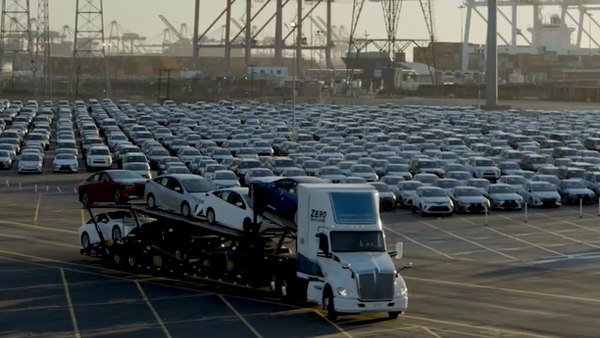
Fuel cell truck at the Port of Los Angeles during a year-long pilot test. toyota
Carbon and Cost
The numerous options and technologies under development for clean trucks will ultimately be sorted out in the market based on cost and carbon footprint.
In terms of cost, whether hydrogen or electric is better for freight “depends on the application and how you’re using it,” says Ahmet Kusoglu, communications officer of the Million Mile initiative and staff scientist at the Lawrence Berkeley National Laboratory in California. “It’s not just how far you go but how often you run continuously.” Hydrogen would be more cost effective, he said, in situations where you have multiple shifts using a vehicle and limited flexibility for downtime.
Those factors have played a role in perhaps the largest current deployment of hydrogen in the freight sector—to power forklifts in warehouses. They are often used around the clock and cannot generate emissions in the enclosed space. There are upwards of 50,000 hydrogen forklifts in the U.S., most previously powered by propane.
Other applications with great potential for cost effective use of hydrogen may be ferries—due to their heavy loads and frequent turnaround—and trash trucks, whose weight and stop-and-go operations can strain battery life. Urban buses may be on the margin since most are candidates for overnight charging. Still, nearly 100 fuel cell buses were under test in eight states in 2021.
While cost is of paramount importance to companies (and transit agencies) seeking to make a profit, the climate crisis and government regulations will make minimizing carbon footprints an important ongoing concern. Based on current technology, hydrogen appears to offer substantial advantages. A study the American Transportation Research Institute comparing zero-emission long-haul trucks across their lifespan—manufacture, energy production and consumption, and disposal/recycling—found hydrogen trucks generate about 20 percent less carbon dioxide than electric trucks (and half that of diesel trucks).
The difference is mainly due to the large amounts of carbon produced in making batteries, including during often dirty mining operations and the need for recycling. (The electric trucks were assumed to require battery replacement at least once during their million-mile life.) “Ultimately, hydrogen trucks are the most environmentally friendly truck type,” said the Institute’s Jeff Short, during a presentation to the North Jersey Transportation Planning Authority’s freight committee in June. That, of course, is based on today’s best estimates—technology and world markets could change it.
Hydrogen Hubs
The prospects for using hydrogen to help power a clean economy are about to get a big boost with the award of federal grants next year to establish five or six regional “Hydrogen Hubs” around the country. The awards come from $8 billion written into the Inflation Reduction Act. The loosely defined “hubs” will span entire states such as California and multistate alliances such as six states in the Northeast stretching from Maine to New Jersey.
Proposals for the hub program are still taking shape but they look to create regional hydrogen ecosystems for supplanting fossil fuels. This includes using hydrogen both as a fuel to generate heat and electricity and taking advantage of hydrogen as a flexible energy carrier—for instance, creating it to store excess energy from solar and wind generation and to supply back-up power for data centers and other energy intensive operations.
Some proposals being developed by mining and oil producing states (such as from the alliance of Utah, Texas, North Dakota and Mississippi) look to advance carbon capture technology to produce and use natural gas-based blue hydrogen.
Numerous companies are lining up to participate, including 60 in the Northeast, many involved in industrial applications such as production of steel, concrete and fertilizers. Finding synergies among applications will be a key focus. In Sweden, Volvo has demonstrated one approach to synergy by using the excess hydrogen produced by a clean steel mill to power its on-the-road heavy duty truck tests.
Despite the flurry of activity in preparing hub proposals, the program has come under some criticism from environmental groups as a “nebulous concept” and for its funding of some fossil fuel-based applications. But it is a new, mostly untried approach for the federal government. In contrast to previous federal programs, “the hubs are focused on demonstration and deployment with less emphasis on fundamental science,” Los Alamos Lab’s Borup said. “It will be exciting to watch.”
Mark Solof is Director of Public Affairs at the North Jersey Transportation Planning Authority.